Digital twins
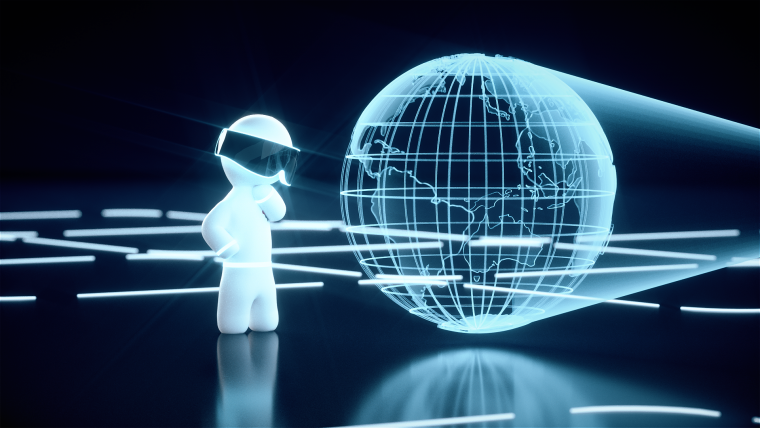
How digital twins are unlocking possibilities across industries
By creating digital copies of physical assets, businesses can optimise performance, reduce downtime, decrease risk, and improve productivity. As a result, digital twins have become increasingly popular across various industries, including: manufacturing, healthcare, and aerospace. Here, we explore the application of digital twins, and how they are being used to give businesses a boost.
Digital doubles for real results
What is a digital twin?
A digital twin is a virtual replica of a physical asset or system. These digital representations of physical objects or systems are used to simulate and predict real world behaviours. Digital twins are built using sensors and data that are collected from the physical asset. These sensors capture data on the asset's performance - such as temperature, pressure, and vibration - which are then used to create a virtual model of the asset.
Digital twin technology uses advanced analytics, machine learning, and artificial intelligence algorithms to simulate the behaviour of the physical asset. This allows businesses to predict potential issues before they occur. Digital twins can also be used to test new designs, simulate changes in operating conditions, and analyse the impact of different scenarios on the asset's performance.
While similar to simulations, there are some key distinctions. A simulation is based on mathematical models that may or may not reflect the actual behaviour of the system being simulated. Models are sometimes also considered an alternative to digital twins. These are simplified representations of a system or process that are used to make predictions or to test out different scenarios. Models can be created using a wide range of techniques, including: mathematical modelling, physical modelling, and computer modelling. They can be used to test the system performance under different conditions, or to explore the effects of changes to a system.
Unlike these other virtual approaches, digital twins are based on real-time data, collected from sensors, IoT devices, and other sources. Digital twins are therefore considered more accurate and reliable than simulations and models, as they are based on actual data rather than assumptions, approximations, and theoretical predictions. While each of these concepts has its own unique strengths and applications, they are all part of the broader trend towards the use of technology to create virtual environments that can be used to improve our understanding of the world around us, and how that applies to business. Whether it's monitoring the performance of a complex system in real-time, or testing out different scenarios with a simulation, digital twin technology is helping us to unlock new insights and possibilities that were previously impossible to achieve.
Digital twin vs. Metaverse
The Metaverse is designed to be a collective virtual shared space, and uses a combination of virtual reality, augmented reality, and other immersive technological approaches. It is a virtual world which people can interact with in real time, using avatars to represent themselves.
It's easy to see how these digital representations of real-life spaces and people share similarities with the concept of digital twins, but they are fundamentally different. Digital twins are focused on replicating physical objects and processes, while the metaverse is focused on creating a virtual space for people to interact with each other and with virtual objects. Digital twins are typically used for monitoring and optimisation, while the metaverse is more focused on entertainment, social interaction, and commerce. Their concepts and applications are therefore markedly different, despite both using a virtualisation approach.
Who uses digital twins?
In the manufacturing industry, digital twins are used to optimise the production process, reduce downtime, and improve product quality. For example: a car manufacturer who uses digital twins can create virtual models of their assembly lines. These models can be used to simulate different scenarios, such as changes in production volumes or the addition of new equipment. By simulating these scenarios, the manufacturer can identify potential issues before they occur, optimise the production process, and reduce downtime.
Similarly, in the aerospace industry, digital twins are used to improve aircraft performance, reduce maintenance costs, and increase safety. For example, an airline may use digital twins to create virtual models of their aircraft. These models can be used to simulate different operating conditions, such as changes in altitude or temperature. By simulating these scenarios, the airline can identify potential issues before they occur, optimise aircraft performance, and reduce maintenance costs.
In the healthcare industry, digital twins are being used to improve patient outcomes and reduce costs. For example: a doctor who uses digital twins can create virtual models of patients. These models can be used to simulate different treatment scenarios, such as the impact of different medications or the effects of surgery. By simulating these scenarios, doctors can identify the most effective treatment options, reduce the risk of complications, and ensure the best approaches are taken for patients.
These are just a few examples of the industries that are embracing digital twin technology and already seeing the benefits.
How digital twin technology helps businesses
Reduced costs
A business owner who uses digital twins can reduce maintenance costs, minimise downtime, and improve operational efficiency. Digital twins allow businesses to identify potential issues before they occur, which can reduce the need for unexpected repairs and costly maintenance.
Improved safety
Digital twins can be used to identify potential safety issues before they occur, reducing the risk of accidents and injuries. By simulating different scenarios, businesses can identify potential hazards and take steps to mitigate them, which not only helps to create a better working environment for employees, but also makes it easier for companies to maintain regulatory compliance with any governing bodies they operate under.
Enhanced innovation
Digital twins allow businesses to test new designs and ideas without the need for physical prototypes. By simulating different scenarios, businesses can identify potential issues and refine designs before they are implemented in the real world. The costs of physical prototyping are significantly reduced, but with no loss of insights, giving businesses more freedom to explore all possibilities, ensuring they reach the best conclusions.
As more businesses continue to adopt digital twin technology, we can expect to see more advances. The integration of Internet of Things (IoT) devices and edge computing will enable businesses to collect and analyse data in real-time, making digital twins even more powerful and accurate. Whether it's through the development of more advanced sensors and data analytics tools, or the use of machine learning algorithms and artificial intelligence, there is no doubt that digital twin technology will continue to play an increasingly important role in shaping business for a long time.
If you'd like to explore how digital twins could enhance your business, get in touch today.
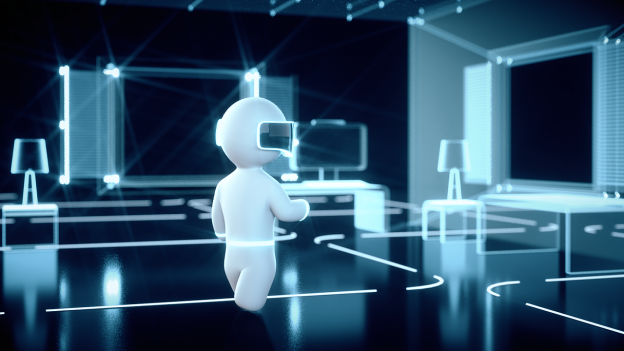
The costs of physical prototyping are significantly reduced, but with no loss of insights, giving businesses more freedom to explore all possibilities, ensuring they reach the best conclusions.